YuriSouder
New member
I have a class for college called "How to build almost anything". I asked if i could build a frame for my jeep and the teacher said yes. i have a 1994 Sahara with a patched, cracked and practically malleable frame.
What are your first thought about this idea?
i have around 40 hours in class to work on this and all the tools i would ever need. What is the best way to begin going about this?
this is how far i got but...
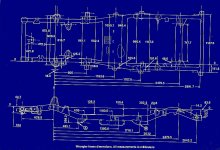
What are your first thought about this idea?
i have around 40 hours in class to work on this and all the tools i would ever need. What is the best way to begin going about this?
this is how far i got but...
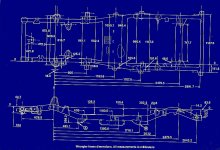